Jet Pumps and HPGL can each deliver high fluid rates. And they can each handle high gas- and sand-flow regimes. Both these conditions are a challenge for ESPs.
So why would you choose one over the other? Let’s look at the benefits and drawbacks of each.
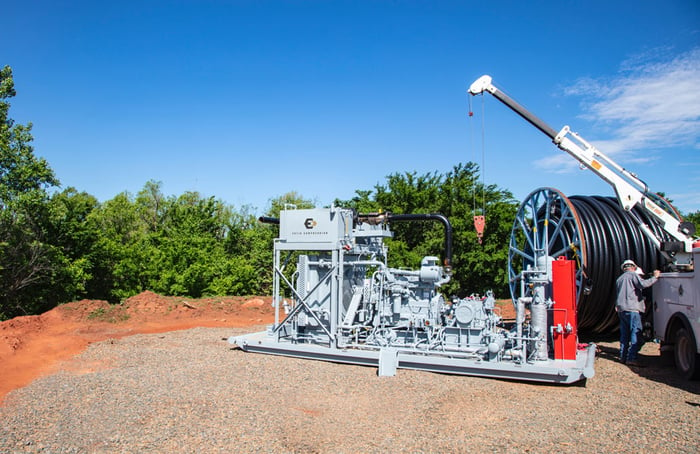
Surface Equipment
Jet Pumps require a surface pump. HPGL requires a compressor. Your uptime comes down to the reliability of your vendor’s equipment.
Surface equipment for Jet Pumps takes up more area, though. You must provide a clean power fluid to avoid plugging the downhole equipment. And trying to get produced water on the wellsite clean enough without having any issues can be challenging.
You may need to chemically treat the power fluid to make sure scale doesn’t precipitate across the equipment, which can also cause plugging. Since this fluid gets pumped at high pressure, any leaks or mechanical failures may cause spills, which could lead to expensive environmental clean-ups.
By contrast, HPGL pushes high-pressure gas down a tubing string. There’s no equipment to erode or get stuck. The limitation with HPGL is you must have gas on site.
Assuming gas is available, let's look at what happens downhole.
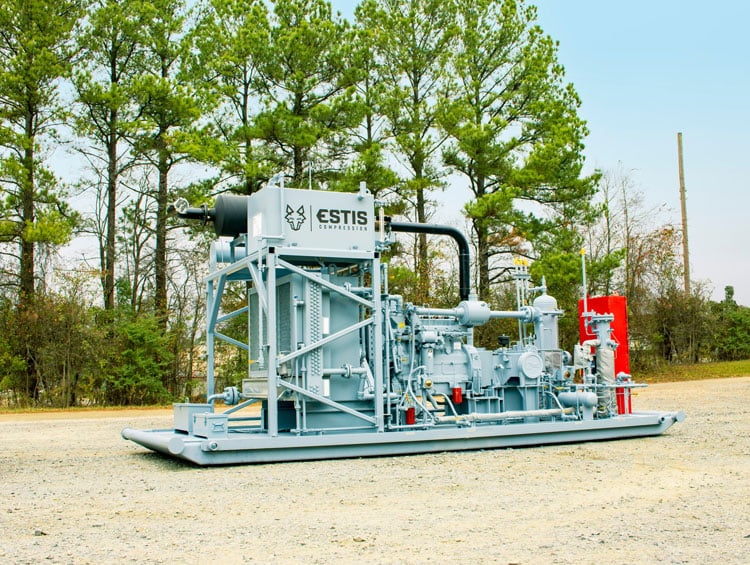
Downhole Equipment
Unlike ESPs, which need a lot of downhole jewelry, neither Jet Pumps nor HPGL requires moving parts downhole. And if the Jet Pump design allows changing out the nozzle assembly without pulling the tubing, you’ll have fewer workovers than if it does not.
Jet Pumps do have some equipment downhole: the packer and the jet pump configuration. The jet pump configuration is contained in the tubing, so it’s easier to manage than an ESP. However, it’s still susceptible to erosion from sand-laden fluids traveling at high velocities. Sand can settle on top of the packer during a shutdown event - which can lead to a stuck packer.
HPGL, on the other hand, uses only a tubing string hung in the wellbore. It’s not susceptible to erosion or other potential failures. HPGL reduces the risk of workovers better than both ESPs and Jet Pumps. Eventually, as the well depletes, you can move over to a gas-assisted plunger lift application.
Operational Efficiency
Because you need a fluid cleaning system, Jet Pumps are typically also more expensive to set up than HPGL.
In addition to possible clean-ups and workovers, Jet Pumps have a lower power efficiency than ESPs or HPGL. They’re also less capable of drawing down wells as fast as other alternative lift systems. Plus, you have less control over the drawdown.
With HPGL, you have complete control over the primary variables that affect drawdown, like flowing wellhead pressure, injection rate, injection depth, and the cross-sectional flow area of the producing flow path. HPGL control gives you increased efficiency.
Jet Pumps are a viable solution in high GLR or high solids production situations…if a gas supply is unavailable.
However, if a gas supply is available, HPGL is a less risky option. Like Jet Pumps, HPGL tolerates high GLRs and high solids production. It also has lower start-up costs, more uptime, and better efficiency.
.png?width=1024&name=image%20(7).png)
Ready to learn more?
Single-point HPGL is the simplest, most efficient and productive lift system with the lowest total cost of ownership and the least downtime.
With companies like Estis making wellhead compression affordable, customizable, and reusable, using HPGL for onshore production is ready to take off. If you’d like to take advantage of this emerging trend, check out our evaluator, to see how you can improve your productivity and reduce costs.
