Which High-Rate Artificial Lift Method is Right for You?
COMPARING HPGL AND ESP IN UNCONVENTIONAL PRODUCTION
More and more operators are looking to high-pressure gas lift (HPGL) for their unconventional wells. It's an attractive option.
HPGL can optimize oil-production rate and recovery during the life of the wells. It's flexible, low cost and simple.
In fact, all that's needed are a tubing string in the well and a compressor at the surface. The compressor provides the high-pressure lift gas.
Since HPGL can achieve high producing rates, it's a viable alternative to the current leading choice for high-rate unconventional wells, the electric submersible pump (ESP). You may wonder if HGPL is the best choice for every high-rate need.
For any application, you must evaluate the well reservoir, fluids and producing characteristics. Only then will you know which artificial lift method will give the best results.
The following six criteria are particularly important when deciding between HPGL and ESP.
HPGL VS ESP CRITERIA 1: HIGH-RATE CAPABILITY
A pilot test published in SPE 195180 documented a rate comparison between an HPGL well and an ESP well. The wells were drilled at the same time in the same area.
The figure below shows the performance of the HPGL well shown on a typical nodal analysis plot of FBHP vs. liquid rate in BBLS/day. The plot also shows the performance of typical offset wells using ESPs.
HPGL outperformed the ESP in early production with higher rates. It did so even though its undersized flow line resulted in higher-than-expected flowline pressures at the high rates.
At day 25, the ESP produced marginally higher flow rates than HPGL. With the right flowline design in the HPGL, however, the difference would've disappeared. The ESP retains a small edge for the next 75 days.
Yet it's clear the ESP is losing its advantage and would lag behind HPGL as it reached its minimum pump intake pressure. This is when the ESP would start seeing head loss from gas interference.
So both HPGL and ESP have high-rate capabilities.
HPGL VS ESP CRITERIA 2: GAS HANDLING
Unconventional oil wells produce a substantial amount of gas. And the percentage of the wellbore occupied by gas increases over time. This happens both from production and because the gas expands as the well is produced due to wellbore pressure drawdown. The table below summarizes the gas oil ratio (GOR) over time for the three largest unconventional oil plays.
The extra gas improves HPGL's performance in most situations. Only when the GOR and reservoir pressure are high enough can lift gas reduce flow. In this condition, the well flows without artificial lift, so adding lift gas can increase friction and decrease well production.
For ESPs, extra gas inhibits performance. With ESPs, all gas must pass by the pump up the annulus or go through the pump. ESP design must consider initial gas volumes and increasing future volumes. Improvements in rotary gas separators and different impeller designs enhance ESP performance. However, it's still difficult to keep the pump at its design capacity as the gas volumes increase over time.
Because of this, HPGL has the advantage over ESPs for most situations.
HPGL VS ESP CRITERIA 3: SAND HANDLING
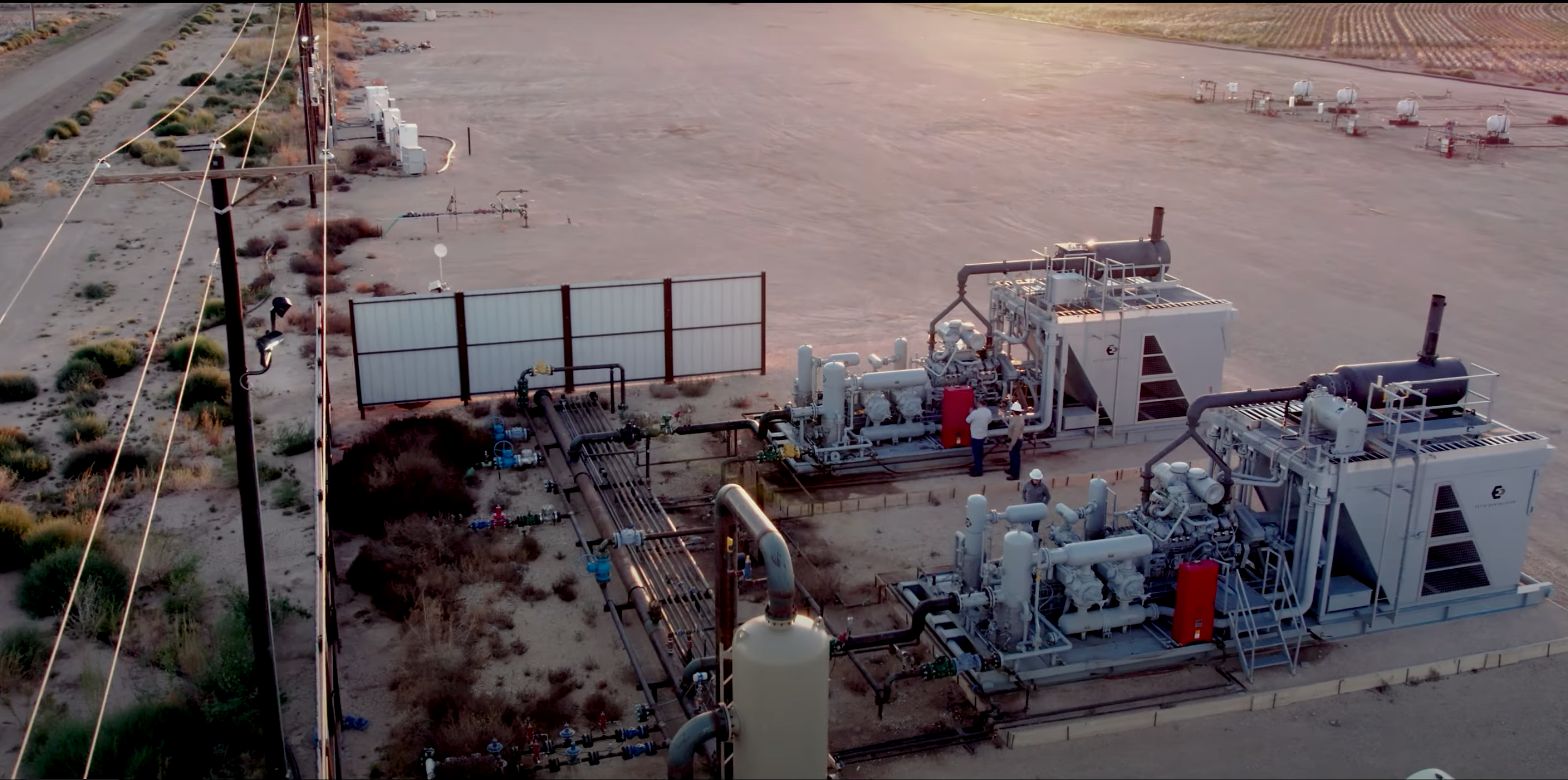
The fracturing of unconventional wells increases the odds of solids, sand and proppant, especially early on. The sand can be very abrasive with tight clearances, producing build-up at any component in the well. Fracture hits from offset wells can also be a source of much sand influx into wellbores.
HPGL's large flow area readily handles any solids in the production stream. Further, the lack of moving parts downhole means there’s nothing to wear out or fight to keep working. Typical fracture hits are not a threat to HPGL wells.
ESP's spin at high speeds with many tight clearances. They can be adversely affected by abrasive wear or solids buildup. To counteract this, ESP's must have abrasion-resistant metallurgy. Yet that still may not prevent pump failure from significant sand production.
Since HPGL is unaffected by solids, it has the advantage over ESPs under solid-laden conditions.
HPGL VS ESP CRITERIA 4: CORROSIVES AND SCALE
Some unconventional wells have a corrosive or scaling environment. This can cause rapid failures in well components and may get worse over time.
HPGL easily transports corrosion or scale inhibitors deep into the wellbore with the lift gas. Alternatively, adjustment to tubular metallurgy can prevent corrosion without inhibitors.
ESP's design must consider the environment. In these wells, it's more difficult to get inhibitors to the bottom of the well. Protection does not reach as deep in the well as compared to HPGL, giving HPGL the advantage.
HPGL VS ESP CRITERIA 5: FLEXIBILITY OVER WELL LIFE
Unconventional wells typically experience a decline rate of 60- 80% per year. Often, compensating for this requires a change in lift type or a change of well components.
HPGL's unique design offers flexibility. It handles high rates with annular flow. Then it can easily switch to tubular flow for lower rates as the well declines. HPGL wells often achieve FBHP's between 300 and 400 psig at low rates. This is comparable with beam pumps, the low-rate lift method of choice. And HPGL does this without the struggle beam pumps face from gas interference or the downtime associated with subsurface failures.
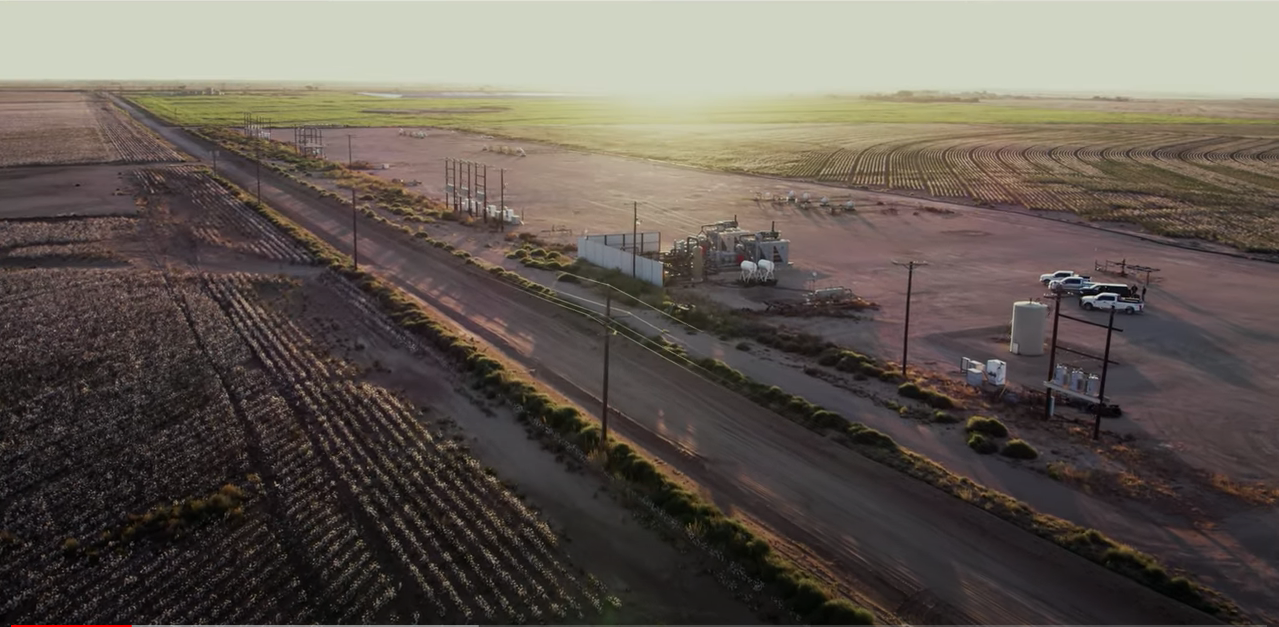
Well operators can also transition from HPGL to plunger assisted gas lift later in the well life. Doing this uses the original string of tubing throughout the well's life. There is some cost to install a bumper spring and plunger wellhead equipment, as well as a short downtime. But there are no rig costs and no need to kill the well.
On the surface, it's only necessary to remove the booster as the well matures.
Tubular sizes and expected system pressures govern the design of an HPGL system. Because of this, HPGL is flexible and works efficiently for nearly any expected well outcome.
ESPs offer less flexibility. Their performance can decline for any installation if the water cut, GOR, or productivity vary from expectations.
They also have limited rate flexibility. Operators need to change at least two or three pump sizes over the life of the well. And because they're inefficient at low producing rates, almost all ESPs get replaced with another artificial lift type late in the well life.
Because of its easy adaptability, HPGL has the most flexibility over the well's life.
HPGL VS ESP CRITERIA 6: OPERATING RELIABILITY
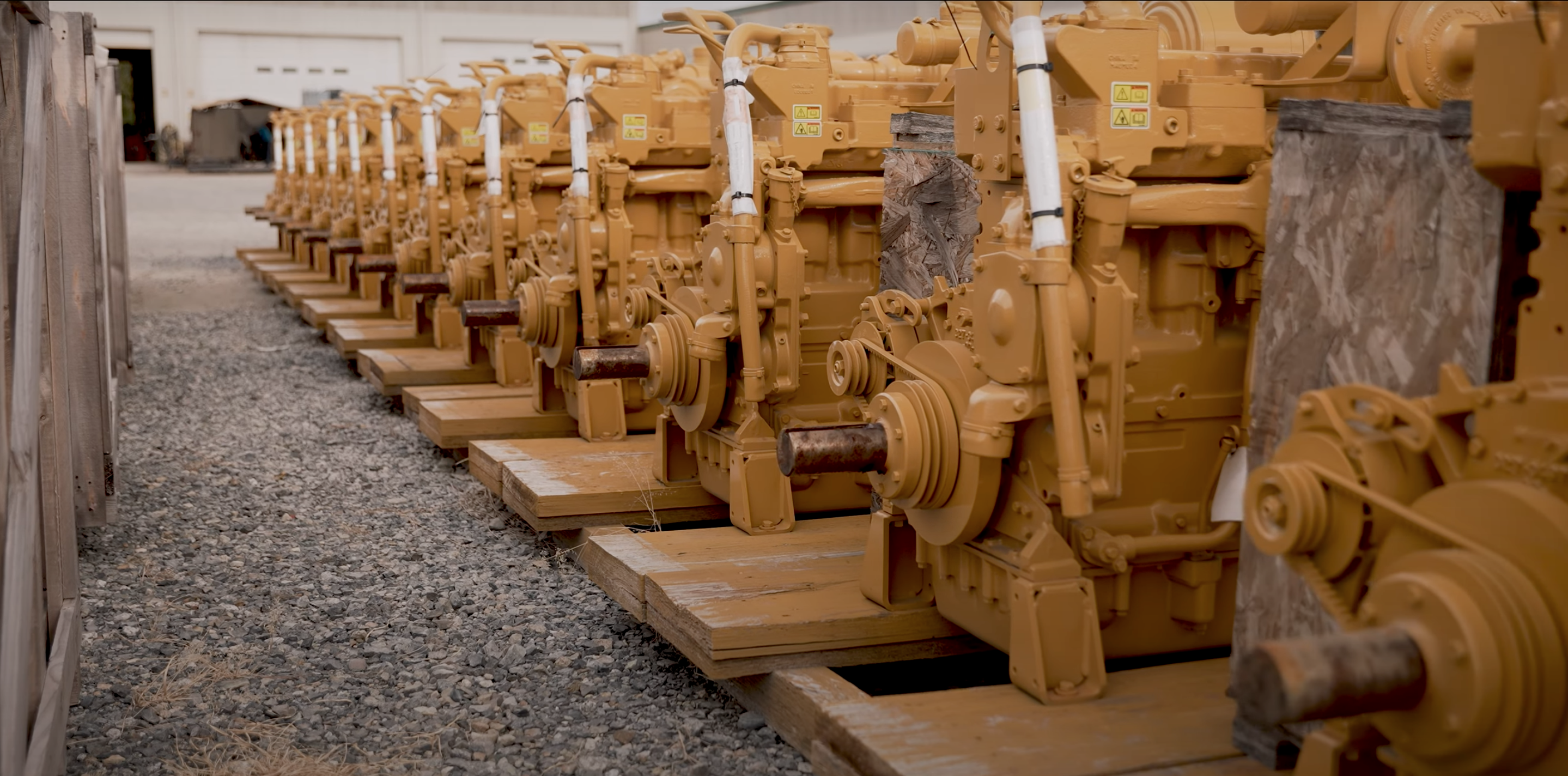
HPGL reliability depends primarily on compressor run time. Quality compression equipment maintained by reliable compression service companies can yield run times more than 99%.
All moving parts--and nearly all potential problems-- for HPGL are above ground. They're readily accessible for repairs and maintenance. Even catastrophic failures can be remedied inside of a day.
ESP systems also depend on their surface equipment. Their generators have similar challenges to compressors. For both HPGL and ESP, a well-designed and maintained system is key to minimizing downtime.
ESPs biggest challenge is the most complicated and vulnerable component: the ESP itself. Pumps are installed more than a mile below ground and can only be accessed via a workover rig. Any failure in the cable feeding power to the ESP or the ESP itself means days of downtime, production loss and high repair costs.
Although all mechanical parts can fail, HGPLs have fewer parts and above-ground access. This makes maintenance and repairs easier, and keeps the entire system more reliable.
HPGL VS ESP CRITERIA 7: ECONOMICS
ESP costs from a Permian Basin operator for their ESP installations were compared to costs for HPGL. The ESP costs include rig work, the ESP itself, a generator (non-electrified field) and its fuel gas. The HPGL costs include feed compressors (allocated for a multi-well pad), compressor installation and fuel costs.
The results of this comparison are below.
As ESP run life in the well increases, the costs for these two lift methods converge. Yet an ESP run life is about 15 months or less. So there's a replacement-cost advantage of about $150,000 per year for HPGL over an ESP. Further, ESP failures are unpredictable and, by nature, inconvenient.
The comparison assumes downtime is the same for both methods, which benefits ESP. It also doesn't account for losses in production from the downtime. Finally, it does not consider limits in production throughout the life of the well.
Considering all lifecycle costs and revenue potential, HPGL has the advantage over ESPs
APPLICATIONS WHERE HPGL IS PREFERABLE TO ESP
Any unconventional well with typical GORs and the capability of producing at high rates is a prime candidate for HPGL.
Wells with GORs that allow them to flow stably on their own are not the best candidates. Nor are wells with low GORs, as described above.
HPGL works well on individual well development schemes. It also performs well in pad developments where the wells can share the feed compressor.
HPGL also operates effectively under uncertainties in early well producing potentials and properties. And it works in either electrified or non-electrified fields. (Note: electrification lowers costs and increases the reliability of both HPGL and ESPs.)
WE'RE HERE TO HELP YOU
At Estis Compression, we want to help our operators get the most value and productivity out of their wells.
We believe HPGL is the best option for many unconventional well applications. Given its low costs, ability to optimize rates and limit downtime, we expect HPGL use to increase dramatically for unconventional wells in the years ahead.
Get in touch and we'll help you decide if HPGL is the right solution for you.
- [ ] artificial lift
- [ ] contract compression
- [ ] compressor packaging
- [ ] HPGL
- [ ] blog
- [ ] article
- [ ] estis compression
- [ ] SWPSC
- [ ] Southwest Petroleum Short Course
- [ ] emissions reduction technology
- [ ] high-pressure gas lift
- [ ] video
- [ ] oil and gas production
- [ ] Estis Cares
- [ ] Permian
- [ ] Scoop/Stack
- [ ] Service Delivery Excellence
- [ ] case study
- [ ] customer service
- [ ] flogistix
- [ ] flowco inc.
- [ ] flowco production solutions
- [ ] gas lift
- [ ] merger
- [ ] unconventional wells